The complete study of the product includes the following activities:
Feasibility study, mechanical functions and aesthetics
The first step in our collaboration with the customer is the feasibility study, evaluating the technical solutions, the choice of the most suitable technology for production, shrinkage and deformation of the raw materials, a rationality study for the efficiency of the mould, optimization of the moulding process, these are only some of the aspects considered before working directly on the component. During this phase we highlight the object's critical points, advancing proposals for improvements or substantial modifications, if necessary. All this is done by our technical office in close collaboration with the customer, creating the foundations of a partnership in development for future projects as well.
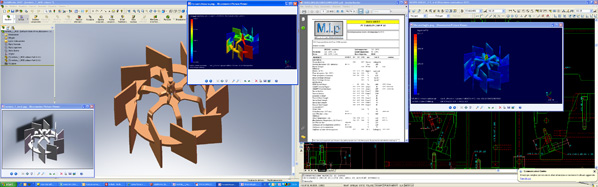
Creating a Mathematical Support for the components in a CAD 3D environment
Following the feasibility study, the second step entails the development of the project in a mathematical and parametric 3D environment, supported by a traditional 2D method. In this phase we exploit the potential of our software which allows us to solve any problems deriving from the engineering of the components, the concourse of complex systems as well as simulations in operational environments, interferences and deformations, with the aim to define the object on a versatile and intuitive support in the agreed time, with the possibility of making the sometimes instantaneous changes imposed nowadays by the market.
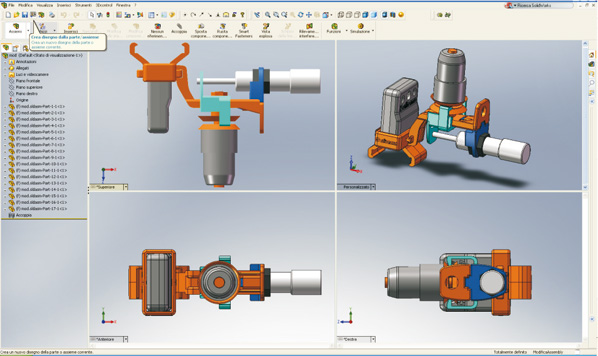
Viewing in photographic rendering
To increase the customer's understanding of the work involved, we exploit the potential of our software with the photographic rendering of the components created. By combining spot light and texture with a variety of customizable plotting, we are able to define the object in space with a far superior perception of the environment than with traditional systems, all favouring, with greater security, an advancement towards the next step in the production process.
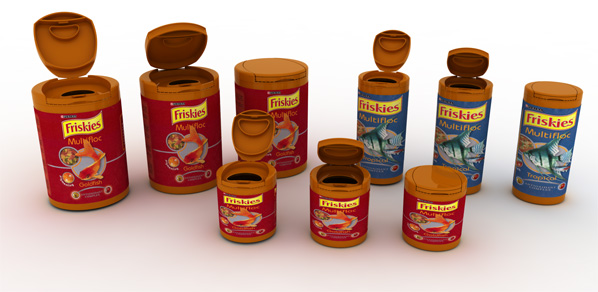
Reverse Engineering of samples or prototypes
For certain projects, the inverse planning process has an absolute value: the customer's viewing of a physical model of the spatial forms and actual operating sizes is followed by the engineered definition by means of 3D models. This process is, in fact, known as reverse engineering. Previously done by the contact of probes, nowadays it is possible using systems such as laser scanning or structured light which interpolated with the software, renders a product identical to the model with tolerances within hundredths, perfectly integrated in the development process.
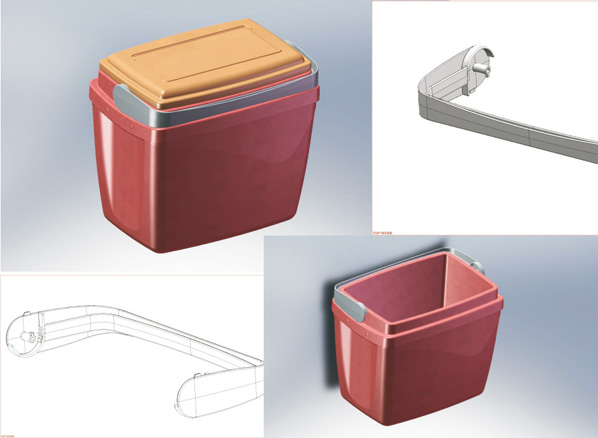
Prototypes
Prototypes have become a necessity for modern companies. Whilst in competitive scenarios an increase in development costs is widely accepted, there is certainly no room for delays in launching a new product on the market. Nowadays the creation of prototypes is common practice, both functional and/or purely aesthetic, allowing a different approach to product development.
The market offers many technologies for the creation of prototypes; we use the most modern and most functional and the wide range of materials now available enable us to develop components that can be transparent or coloured, resistant and flexible. Thanks to our long-standing experience in this sector, we are able to suggest the best technology and the most suitable material to achieve the desired result.
For the creation of prototypes, we can offer the following technologies:
- SLA (StereoLithographic Apparatus)
- Multi Jet Modelling (MJM)
- (Selective) Laser Sintering
- Fused Deposition Modelling (FDM)
- Selective Laser Melting (SLM)
- CNC finishing (CNC milling)
- Silicone moulds for small series max 40 pcs
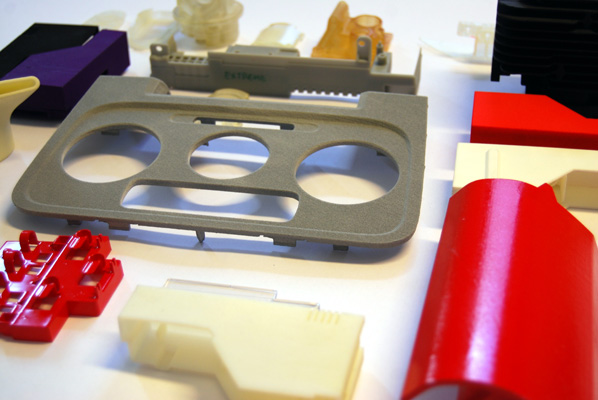
Quotations for moulds and moulding
Mould design involving all parties concerned with the order
The design and construction of moulds represents the core business of our activities. 30 years' experience in the plastic moulding sector has allowed us to gained enormous skills in making moulds to suit all technical specifications. The limits to design and to construction are ever evolving, and besides consolidated standards such as traditional moulds, thanks to new technologies we now find even more complex equipment such as multi-cavity moulds, with multiple hot chambers, inclined, sequential, shut-off moulds, moulds for over-moulding steel-plastic, plastic-plastic, plastic-plastic-rubber, for manual or automatic loading, sandwich moulds, rotating moulds, transfer moulds on machines provided with automatisms integrated in the equipment, IML and IMD systems.
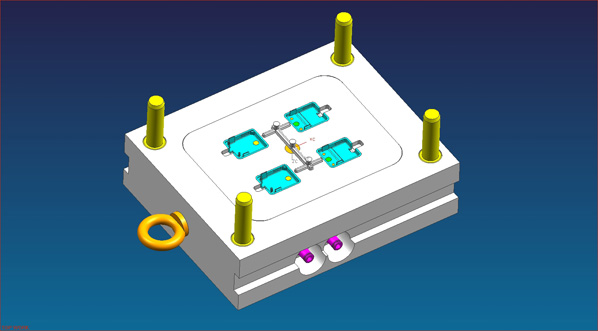
Mould construction using the most modern technologies (CNC 3-5 axis, Wire erosion, etc.)
Mould construction is MIP's core business, together with design. Even if we wrote reams, we still would not be able to describe the great experience we have accumulated in 30 years of activity during which we have faced and overcome many problems with tenacity and capability, collaborating and cooperating continuously with customers who enjoy the benefit of the equipment we build. We can say that if we still exist after 30 years, still doing the same job, then we have achieved something positive...
Every year we plough part of our income back into the company to implement the production department with the most modern CNC 5-axis machines, even more sophisticated software, and to train our staff so they can readily answer the many problems put forward.
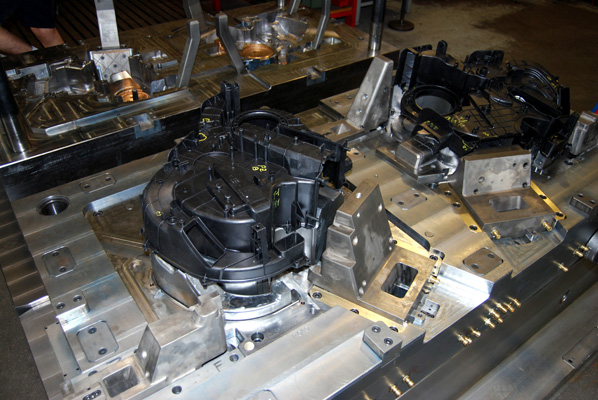
Moulding of samples, preproduction or batches (bi-materials, gas, IML, etc.)
Thanks to our partners we can provide the service of moulding plastic materials using 2 types of technology: injection moulding and blow moulding. They are very different but perfectly integrated in the production of complex items.
Injection moulding is an industrial production process in which the plastic material is melted and injected at high pressure inside a closed mould which is opened when the item is cold.
Generally the injection is done at very high pressure and at high temperatures to allow the "plastified" material to flow easily through the machine.
Blow moulding is a process used to obtain hollow plastic objects (bottles or jars, for example).
Blow moulding is done by blowing compressed air inside a preform or parison positioned inside a hollow mould so that when it is "blown up" the object takes on the form of the inside wall of the mould. The object is then cooled and the mould is opened to remove the finished item.
The preform or parison can be made on-site using an extruder coupled to the blowing machine (therefore in the same plant) or they can be made separately in another plant.
Thanks to our partners' very high technical skills, we can mould any plastic material, from the more common (PP, PE, PS, ABS, PA6-66, PC, PMMA, etc..) to those more technological (PSU, ULTEM, PBT, PA+GF, PA+CF, POM, etc...)
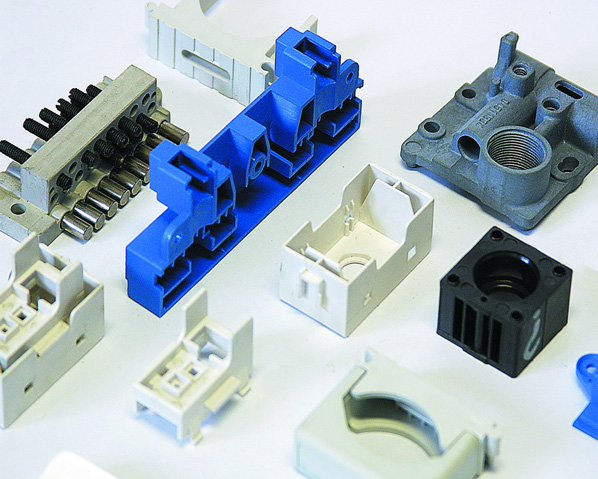